Como dicen los anglosajones, este es un “side project”, esto es, un proyecto que hacemos en nuestro tiempo libre, aunque este año nos hemos propuesto terminar la moto y por ahora parece que vamos bastante bien encaminados para conseguirlo.
El truco es dedicarle todos los días un rato, aunque sea pequeño.
Ahora mismo la moto tiene este aspecto:
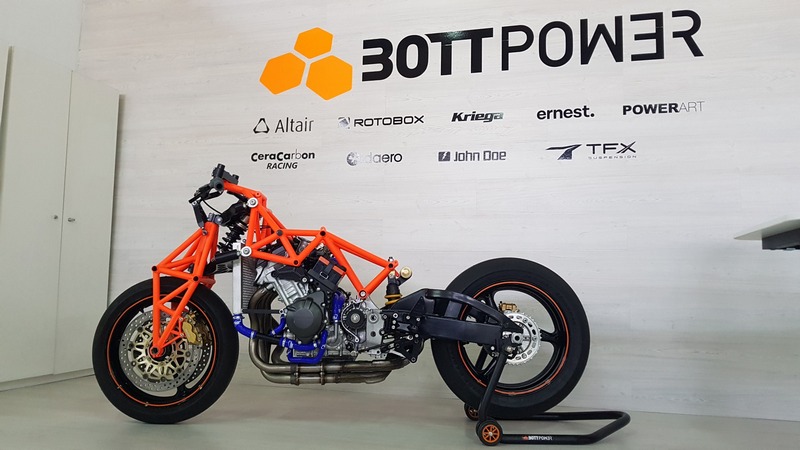
Le hemos montado manguitos de silicona en el sistema de refrigeración. Hemos sujetado el radiador en la parte inferior con unos tirantes de fibra de carbono, hemos montado unas estriberas nuevas, la palanca de embrague, el puño de gas.
También hemos impreso un primer prototipo del airbox, que encaja bien en la moto.
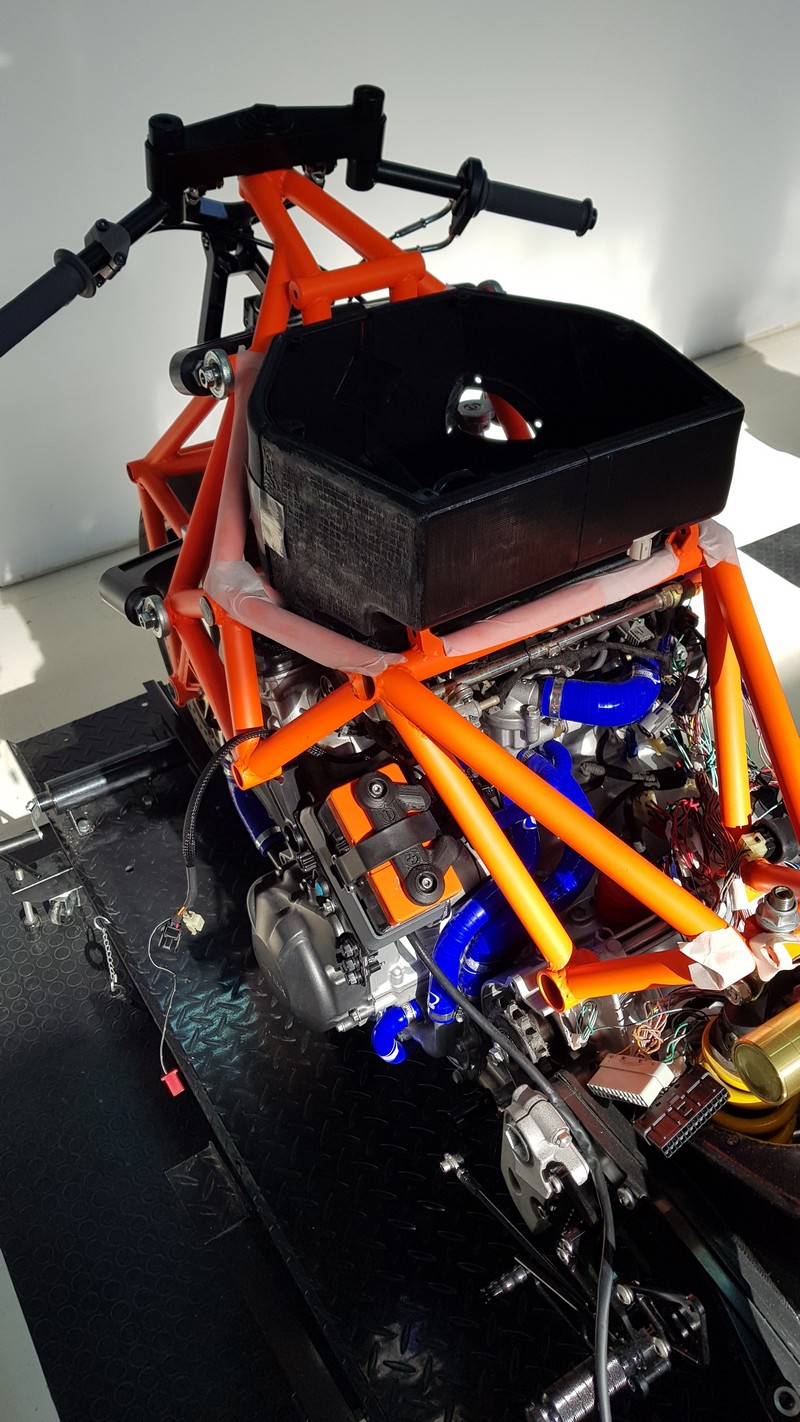
Con respecto al depósito de gasolina, hemos llegado a un acuerdo con la empresa estadounidense Pyrotect que está especializada en la fabricación de depósitos de gasolina para vehículos de competición, sobre todo coches. Sus depósitos cumplen con la normativa de la FIA (Federación Internacional de Automovilismo).
Constan de una bolsa que contiene la gasolina, que a su vez está dentro de una carcasa que puede ser de aluminio o de fibra de carbono. La siguiente imagen muestra uno de estos tanques, con una caja de aluminio y la bolsa que se pone en el interior.
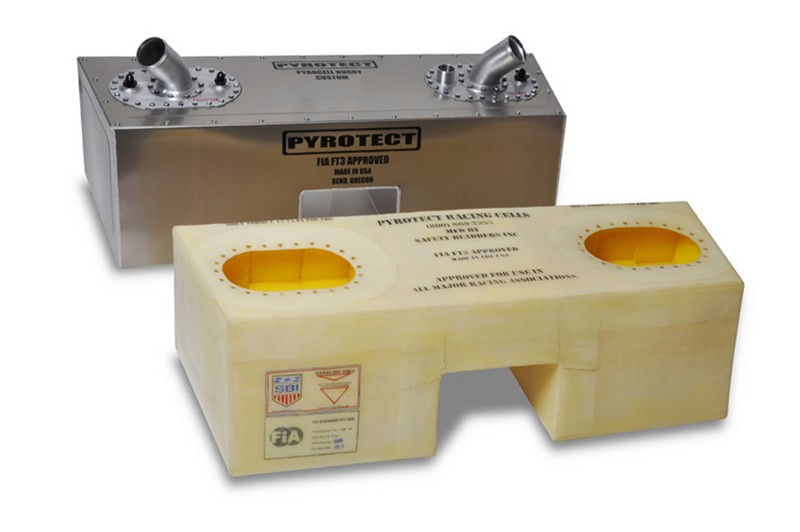
La idea es que Pyrotect nos fabrique una bolsa a medida para el depósito de la Morlaco y nosotros fabricaremos la carcasa exterior, que tendrá la misma forma que en los renders.
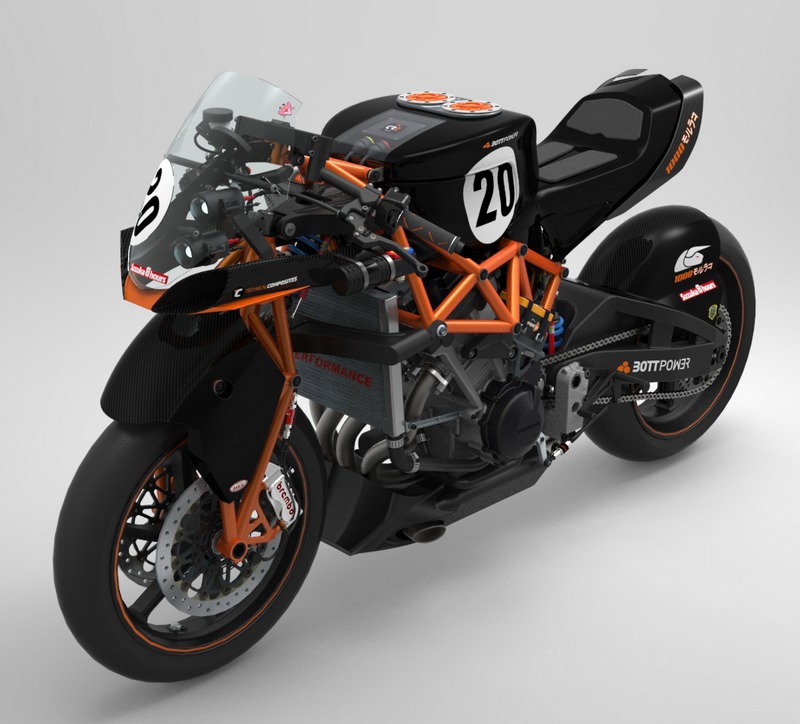
La bolsa proporciona un nivel de seguridad altísimo en caso de impacto y además se elimina el riesgo de fuga de combustible debido a grietas, fisuras, etc. Creemos que con esta tecnología vamos a ser capaces de aumentar mucho el nivel de seguridad de nuestros depósitos de gasolina con respecto a un depósito de gasolina convencional de moto hecho de chapa de aluminio o acero.
Esta es una solución que vamos a desarrollar en este primer prototipo de la Morlaco y que queremos aplicar en las siguientes motos que diseñemos.
Estos días también estamos trabajando sobre todo en el diseño del morro de la moto.
Ya tenemos la cúpula Ermax que vamos a montar:
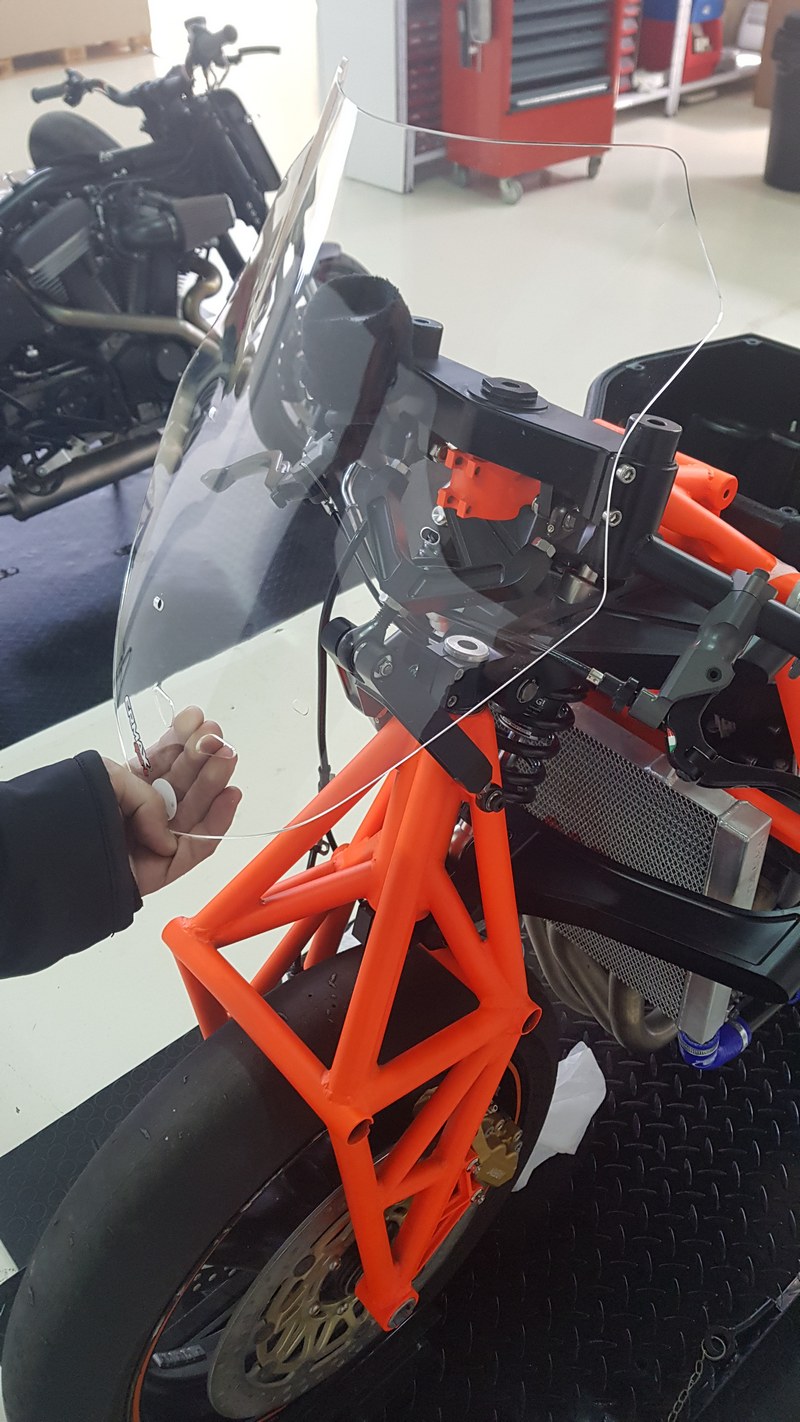
También los faros, de la marca estadounidense Denali. Son muy pequeños, ligeros y con tecnología led.
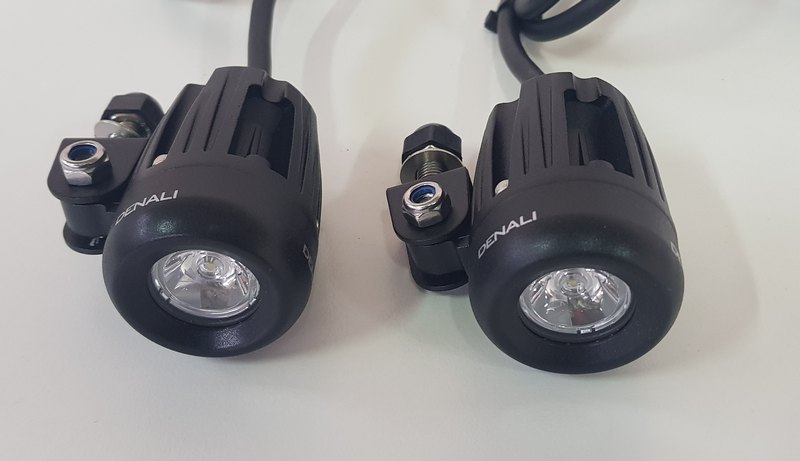
También tenemos el tacómetro. Vamos a montar esta unidad de Speedhut, nos gusta porque tiene un diseño muy racing y es muy simple y ligero.
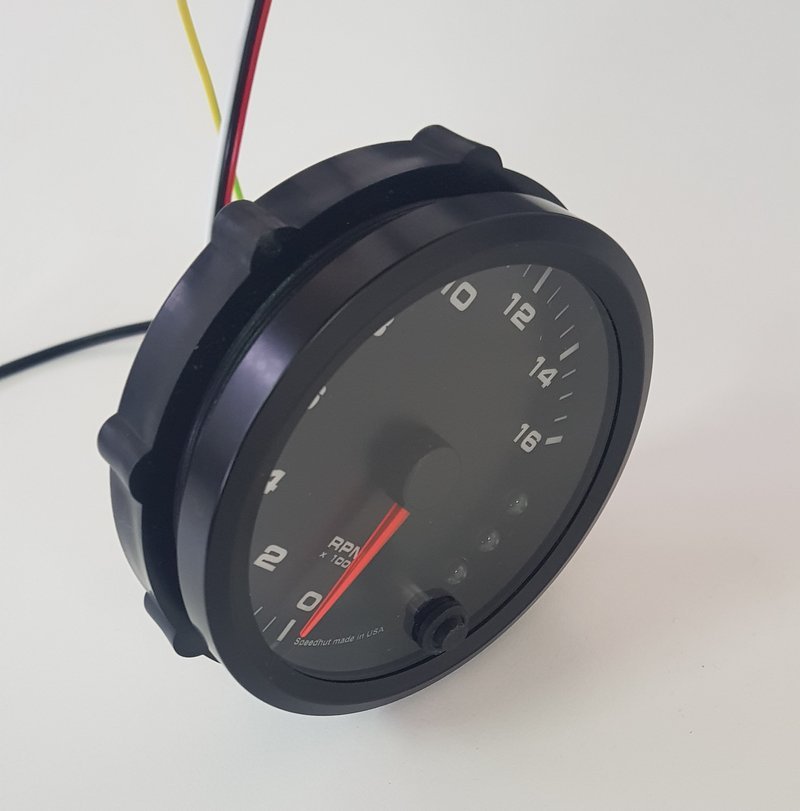
Para sujetar todos estos elementos (cúpula, faros, tacómetro) estamos pensando en hacer una pieza impresa en 3D, que llamamos “araña”. La araña probablemente tendrá una forma bastante orgánica. La queremos diseñar utilizando el software de optimización topológica de Altair.
Rémy Roland, el estudiante de diseño industrial que estuvo unos meses de prácticas con nosotros, durante los cuales diseñó una concept bike eléctrica para correr en Pikes Peak, está haciendo bocetos para darnos ideas sobre el aspecto general que podría tener la araña. Ya puestos, también nos está dando ideas para el guardabarros delantero.
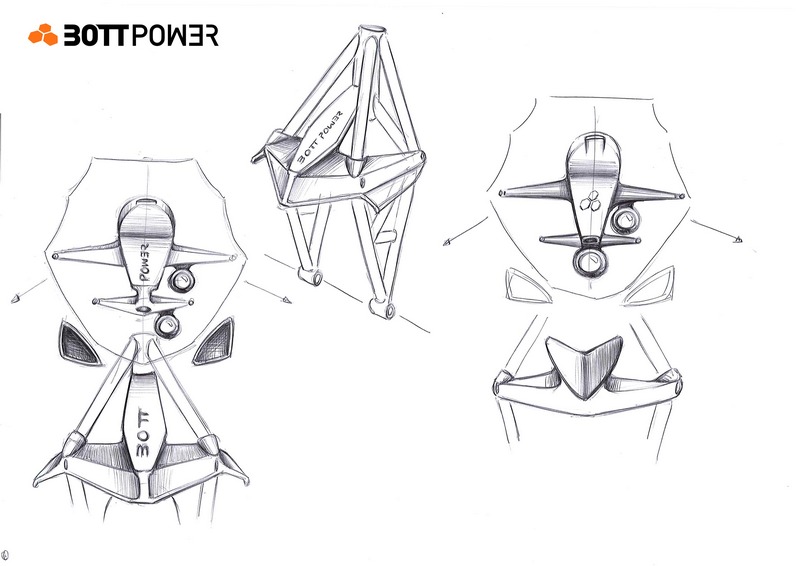
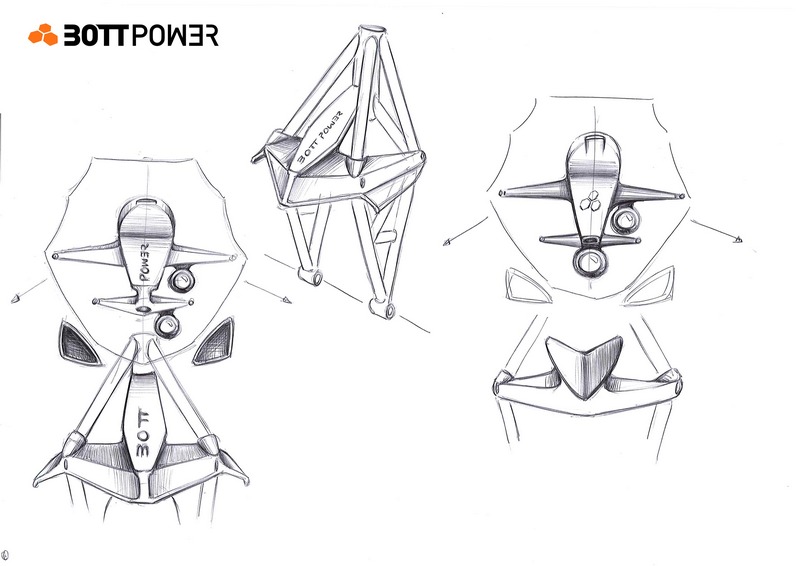
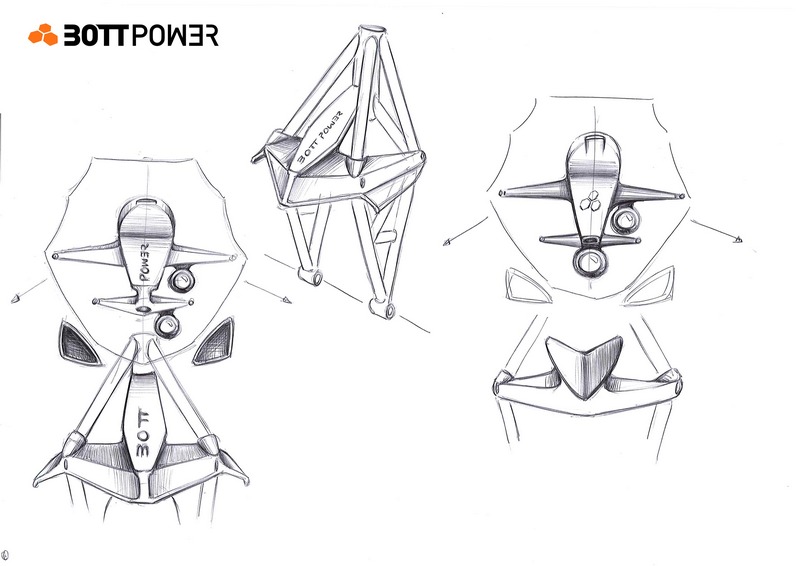
Todavía no hemos decidido por dónde irán los tiros repecto al diseño final, estamos en ello.
Esta pieza puede ser una buena oportunidad para emplear una estructura de tipo Lattice, que son estructuras intrincadas que utilizan una cantidad mínima de material para llenar un volumen, a la vez que proporcionan rigidez estructural. Este tipo de estructuras están formadas por celdas repetitivas y la fabricación aditiva (impresión 3D) es la tecnología ideal para construirlas.
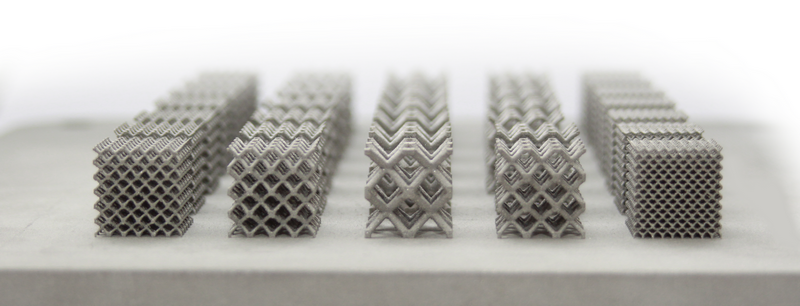
Lo interesante de las Lattice es que dentro de la pieza se puede variar la densidad de la estructura, de forma que sea más densa en los lugares donde los niveles de tensión sean mayores y menos densa donde las tensiones sean menores. De esta forma se puede obtener una pieza muy optimizada en la relación peso/rigidez. La siguiente imagen muestra una prótesis de un fémur, seccionada. (imagen cortesía de Betatype, http://www.betaty.pe/services/ ).
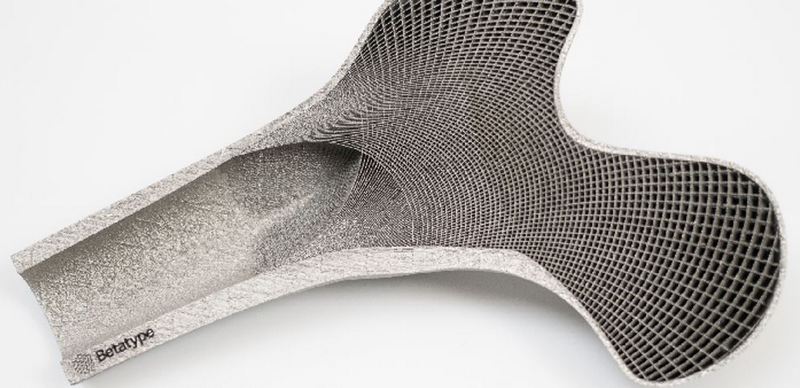
Nos estamos divirtiendo mucho con este proyecto. Seguimos avanzando y ¡seguro que en unas semanas tendremos más cosas nuevas que contar!. 🙂